Maintenance Management
Maintenance management involves planning, coordinating, and overseeing all activities related to asset upkeep in an organization. Its goal is to keep assets in peak condition, minimizing disruptions, maximizing reliability, and prolonging their lifespan. Effective maintenance management is essential for upholding efficiency, cutting costs, ensuring employee safety, and maintaining business operations.
Maintenance management goals focus on maximizing equipment dependability, minimizing downtime, reducing maintenance expenses, and optimizing maintenance resources. Maintenance managers can contribute to the company’s prosperity by aligning maintenance tasks with objectives.
Advantages of Maintenance Management
Maintenance management provides advantages to businesses. It aids in prolonging the life cycle of assets, enhancing productivity, boosting safety measures, decreasing breakdowns, and enhancing customer satisfaction. Furthermore, it facilitates resource planning and utilization, resulting in cost savings and increased profitability.
There are different types of maintenance in manufacturing, including reactive maintenance, calendar-based maintenance, usage-based maintenance, condition-based maintenance, predictive maintenance, and prescriptive maintenance. Preventive maintenance is a formalized program used within manufacturing to optimize and extend the life cycle of production equipment.
When deciding which maintenance strategy to deploy, there are various costs to consider. Part costs, technical labor, and other maintenance-related materials can make maintenance quite expensive. In every strategy, there are trade-offs between the level of factory maintenance and the costs involved.
Types of Maintenance in Manufacturing
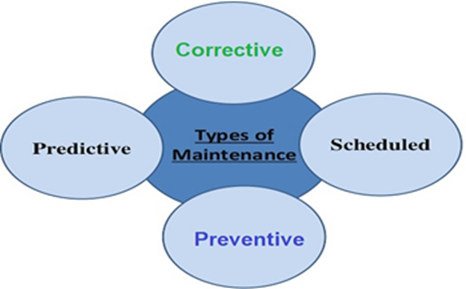

Reactive Maintenance:
When it breaks, you fix it.
Preventive Maintenance:
You schedule replacements ahead of time before parts break, usually at a regular interval.


Usage-Based Maintenance:
You replace parts when the machine has been used a certain amount before they break.
Condition-Based Maintenance:
You replace the parts when they seem like they are getting too worn out to continue to function appropriately.

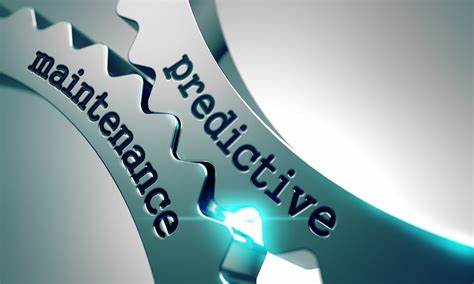
Predictive Maintenance:
You utilize historical data to make predictions about when a part will break and replace the parts based on these predictions, prior to them breaking. This usually, but not always, utilizes artificial intelligence and machine learning.
Prescriptive Maintenance:
Advanced data analysis methods are used to do more than predict failure points, but instead provides hypothetical outcomes in order to choose the best action that can be taken prior to failure, safety hazards, and quality issues arise as well as the timing of implementation.
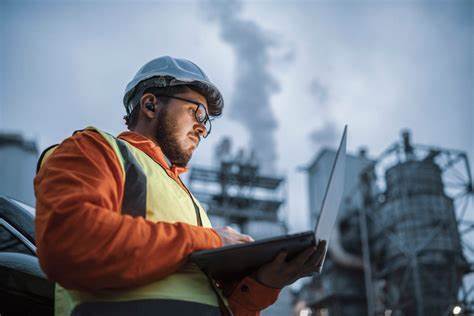
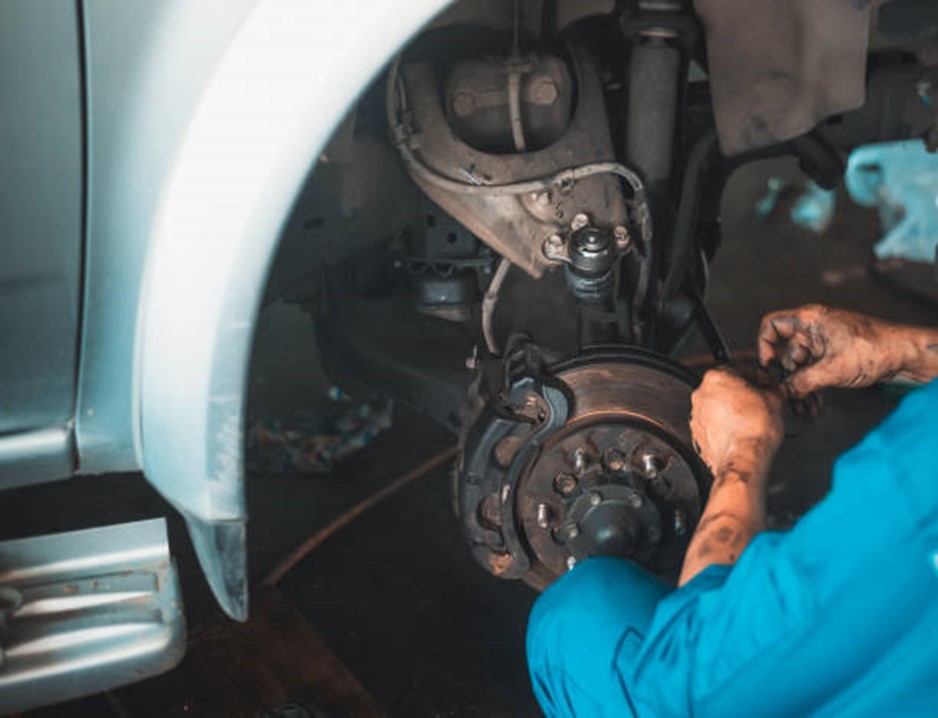
Breakdown Maintenance
When a machine suffers an unplanned stop due to a breakdown, the maintenance team swings into action. Repairs may include temporary solutions to get the equipment going until the next changeover or until a part arrives. Maintenance technicians may also use corrective maintenance to ensure the problem doesn’t happen again.
Planned Maintenance
Many maintenance strategies involve planned maintenance, such as preventive maintenance, conditions-based maintenance, and predictive maintenance. Each company must determine the most appropriate maintenance strategy for its operations.

Planned maintenance includes service, wear and tear, consumables, and other machine health-related tasks. It utilizes a maintenance plan that covers as many planned tasks as possible at the lowest cost.
Planned maintenance tasks include:
- Oil changes
- Lubrication
- Belt tightening and replacement
- Change of consumables
- Setting adjustments
- Deep cleaning
- Electronics checks
- Diagnostics